En el entorno competitivo actual, contar con una metodología para el diseño de la cadena de suministro es un factor determinante para el éxito de cualquier fabricante con una red de distribuidores. La configuración de la cadena de suministro no solo define la estructura de esta, sino también las interconexiones secuenciales entre los componentes del sistema, como la localización de instalaciones, las políticas de producción, y la asignación de recursos de distribución y modos de transporte.
Al abordar el diseño de esta metodología, es crucial considerar tanto decisiones estructurales, como la ubicación y capacidad de las instalaciones, como decisiones de coordinación, la selección de proveedores, elegir un software base para la distribución logística y la asignación de inventarios. Este enfoque integral busca optimizar el rendimiento de la cadena de suministro, logrando un equilibrio entre la eficiencia de costos y la capacidad de respuesta.
En este artículo, exploraremos las metodologías clave para el diseño de la cadena de suministro en un fabricante que opera con una red de distribuidores, con el objetivo de identificar la configuración que maximice el desempeño y la competitividad en el mercado.
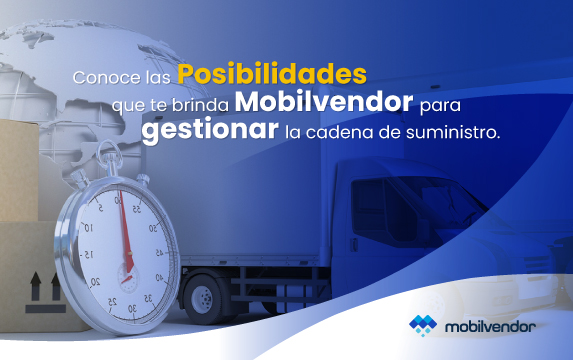
¿Cómo diseñar una cadena de suministro en un fabricante con red de distribución?
El diseño de una cadena de suministro eficiente para fabricantes con redes de distribuidores es fundamental, especialmente ante problemas comunes como la falta de coordinación, visibilidad limitada, problemas logísticos y una gestión ineficiente de inventarios. Estos obstáculos pueden resultar en demoras en la entrega, costos elevados y una menor satisfacción del cliente.
Para enfrentar estos retos, es fundamental considerar siete decisiones clave en el diseño de la cadena de suministro:
- La elección entre fabricar o comprar (outsourcing).
- La selección de proveedores.
- La política de planificación de producción.
- El modo de transporte.
- Las decisiones de localización.
- La capacidad de las instalaciones.
- La asignación de producción y servicios.

La relación entre estas decisiones exige un enfoque integral para optimizar el rendimiento y reducir costos en todo el sistema.
Mobilvendor ofrece soluciones específicas para superar estos desafíos sin intervenir directamente en los procesos de producción, pero integrándose de manera eficaz con los sistemas ERP existentes (Conoce las integraciones de Mobilvendor aquí). A través de la sincronización en tiempo real, optimización logística y análisis de datos, se logra una cadena de suministro más coordinada y visible, permitiendo que los fabricantes aseguren la disponibilidad de productos, reduzcan costos operativos y mejoren la satisfacción del cliente.
Estas herramientas no solo potencian la eficiencia en la gestión de inventarios y la logística, sino que también proporcionan a los fabricantes la capacidad de responder rápidamente a fluctuaciones en la demanda, garantizando un flujo de operaciones más fluido y efectivo en toda la red de distribuidores.
Metodología que puedes emplear para diseñar la cadena de suministro
A continuación, te vamos a presentar una metodología de diseño de cadena de suministro basada en el modelo de programación entera mixta MIP.:
Modelo de programación entera mixta MIP
El modelo de programación entera mixta (MIP, por sus siglas en inglés) es una herramienta matemática utilizada para diseñar la cadena de suministro de una empresa de fabricación con una red de distribuidores. Este modelo ayuda a tomar decisiones óptimas sobre la localización de plantas y almacenes, las capacidades de producción, y el flujo de materiales a lo largo de las diferentes etapas de la cadena de suministro.
Básicamente, se codifican en un cromosoma las políticas de producción y los modos de transporte que cada empresa en la cadena llevará a cabo. A partir de ahí, el modelo MIP, con la ayuda de un software logístico, backoffice y de análisis de datos, resuelve para determinar las mejores ubicaciones para las plantas y almacenes, así como las capacidades necesarias en cada instalación para satisfacer la demanda. Aquí podemos ver un ejemplo simple de su funcionamiento:
Objetivo: Minimizar el Costo Total (TotalCost)
Desglose de la fórmula:
- Costo fijo de inversión (FixCost): Costo asociado a la apertura de una planta o almacén en la ubicación i.
- Variable binaria Xi : Indica si la planta o almacén en la ubicación i está abierta (1) o cerrada (0).
- Costo variable de operación (VarCost): Costo asociado a operar la capacidad Cap_i en la planta o almacén en la ubicación iii.
- Capacidad cap_i: Capacidad operativa de la planta o almacén en la ubicación iii.
- Costo de tansporte (TransCost): Costo por transportar materiales o productos desde la ubicación i a la ubicación j.
- Flujo de material Yij: Cantidad de material o producto transportado desde la ubicación iii a la ubicación jjj.
Ejemplo real:
Supongamos que tienes dos ubicaciones posibles para plantas (A y B) y dos posibles almacenes (X y Y). La fórmula te ayudaría a decidir cuáles abrir, qué capacidad asignarles, y cómo mover productos entre ellas para minimizar el costo total.
- FixCost_A = $100,000 (Abrir planta A)
- FixCost_B = $150,000 (Abrir planta B)
- VarCost_A = $50/unit (Costo variable en planta A)
- VarCost_B = $60/unit (Costo variable en planta B)
- TransCost_AX = $10/unit (Costo de transporte de A a X)
- TransCost_BY = $15/unit (Costo de transporte de B a Y)
Aquí, el objetivo es elegir (1 si abres, 0 si no) y las cantidades , , , que minimicen el costo total.
Conclusión
Diseñar una cadena de suministro eficiente para una empresa de fabricación con una red de distribuidores implica tomar decisiones estratégicas y complejas que abarcan desde la ubicación de instalaciones hasta la política de producción y los modos de transporte.
El implementar un modelo como el MIP, ayuda a minimizar el costo total del sistema al considerar variables como costos fijos y variables, costos de transporte, y costos de inventario. Sin embargo, debido a la naturaleza compleja y a menudo no lineal de estas decisiones, se requiere un enfoque que combine algoritmos genéticos, programación mixta y simulación para obtener resultados precisos y prácticos.
En este contexto, Mobilvendor se presenta como una solución clave para enfrentar los desafíos típicos en la gestión de cadenas de suministro. Mobilvendor ofrece sincronización en tiempo real, optimización logística y análisis de datos que ayudan a mejorar la coordinación, aumentar la visibilidad y gestionar eficientemente los inventarios. Si quieres conocer más de cómo Mobilvendor se integra en tu proceso de transformación de la cadena de suministro contáctanos aquí